
[ad_1]
Take heed to this text |
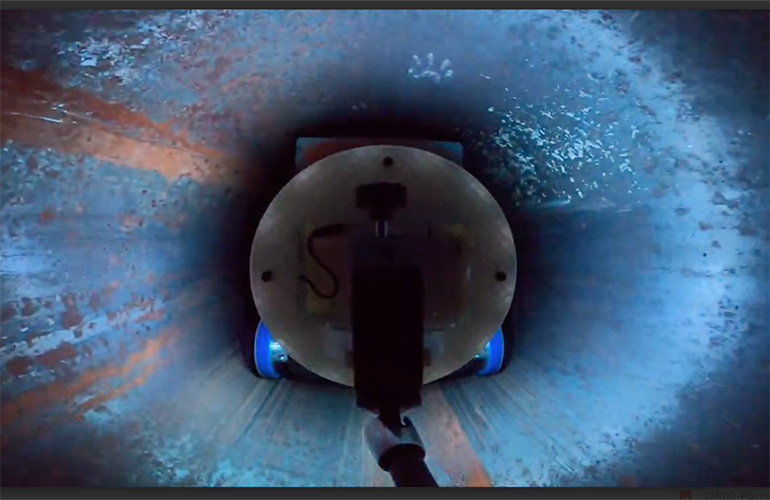
CMU pipe-repair robots crawl into pure gasoline pipelines and coat them. | Supply: Carnegie Mellon College
Researchers at Carnegie Mellon College’s Robotics Institute are creating robots that may map and restore pure gasoline pipelines. The workforce is led by Howie Choset, the Kavčić-Moura professor of laptop science at CMU, who plans to commercialize the robotic later this 12 months.
The CMU workforce’s modular robots crawl inside pure gasoline pipelines to map the traces, detect decrepit or leaking pipes, and restore them by making use of a resin coating alongside its internal wall. Underground pipelines carry pure gasoline to 75 million houses and greater than 5 million industrial clients within the U.S., in response to the U.S. Division of Power (DoE).
This gasoline is carried via a community of 1.2 million miles of distribution principal traces and 900,000 miles of service traces. These pipes are costly and troublesome to restore. They’re too small for people to suit into, and a few are so outdated that they’ve by no means been mapped. If left unattended, nonetheless, the pipes will proceed to decay.
“We’re going to see pipes bursting extra usually, we’ll begin speaking about traces taking place increasingly more usually, as a result of we’re not going to be proactive in addressing our pipe infrastructure,” Choset instructed The Robotic Report.
“The pipe networks in america are decaying, and we have now to interchange or restore them,” he mentioned. “We don’t even know the place the pipes are or the standing of those pipes, so the very first step is simply mapping the place the pipes are.”
Challenges include work in tight areas
Choset’s workforce at CMU Robotics Institute has specialised in snake robots previously. That is what put it on the radar of the DoE, which is sponsoring the challenge via the Superior Analysis Initiatives Company-Power and its Speedy Encapsulation of Pipelines Avoiding Intensive Substitute program.
“Individuals reached out to us due to our work with snake robots, however as a result of pipes are comparatively well-structured environments, we had been in a position to make robots that had been particular to the pipe surroundings,” Choset mentioned.
As a substitute of constructing a snake robotic, Choset and his workforce determined to create a crawling robotic.
“We constructed some pipe-crawling robots, and we definitely should not the primary to construct pipe-crawling robots,” Choset mentioned. “However what makes ours totally different from others is that they’re very robust. They will carry a heavy weight. They’ve the potential, and I stress that phrase ‘potential,’ to do some form of restore. The present functionality that we’re very pleased with is mapping, that’s the primary essential step.”
The CMU workforce’s robotic sits on a pair of 2-in. wheels and has a 3rd wheel atop the module. The robotic has three wheels as a result of each the pipe-repair resin and the batteries that energy the robotic will be heavy, so it must have sufficient traction to drag as much as 60 lb. of payload.
The robotic can examine about 9 miles of pipe in eight hours and might restore about 1.8 miles of pipe in the identical period of time.
To construct these robots, the CMU workforce couldn’t use typical sensors, like lidar and radar, in order that they developed a high-resolution optical sensor that might work in tight areas. Choset mentioned he’s at present looking for a patent for these sensors.
“The mere physics of how these sensors work don’t lend themselves properly to being in a decent area,” Choset mentioned. “We found out how one can create lidars and imaginative and prescient techniques that work in tight areas.”
The sensors the workforce constructed ended up being much more correct than they predicted, in response to Choset. The workforce has had promising outcomes with its exams.
“Not solely are we attempting to create a geometrical map of the pipe that claims, ‘Right here’s a tube, there’s a tube, right here’s how the tubes connect with the maze,’ so to talk,” Choset mentioned. “We’re additionally texture mapping what the inside of the pipe seems to be like onto these maps that we’re creating.”
How the robots restore pipes
Whereas vital, mapping is simply a part of these crawling robots’ capabilities. The CMU workforce has geared up them with a module that has a spinning nozzle. This nozzle applies resin as a steady bead that spirals alongside the pipe wall because the robotic inches alongside.
“Our companions labored with the College of Illinois to develop a resin sort of goo or Vaseline-type substance, that you just carry with the robotic and also you deploy it at websites the place the pipe is in disarray,” famous Choset. “The goo hardens, after which basically you could have a brand new pipe inside a pipe.”
Regardless of the workforce’s success with this facet of the challenge, it has been derailed as a result of the DoE is not sponsoring the restore facet of the work, Choset mentioned. In accordance with him, a change in program administration on the DoE has left issues unsure, though its nonetheless an vital facet of the work for him.
“What I’m doing is scraping collectively no matter leftover assets I can discover it proceed this challenge,” Choset mentioned. “To not say it’s my pipe dream, as a result of that might be form of humorous, however this is a crucial drawback. The fact is in 50 years, we’re not going to have pipes.”
As well as, the workforce is amassing information that it plans to make use of to construct a machine-learning algorithm to have the ability to assess injury by itself.
“Proper now, [the robots] acquire visible information, and somebody seems to be at it. What we need to do is assist automate that course of by cataloging identified forms of injury, cracks, and rusts, and have the robotic mechanically flag the place they’re,” mentioned Choset. “The issue is, with most machine studying algorithms, you want information to coach the method, and we don’t have that information.”
“The info we’re amassing to create these maps goes to function the premise for, basically, higher-level synthetic intelligence,” he mentioned. “So not solely do we have now a pipe community, we have now, probably, a time-varying pipe community. After which we have now one the place a synthetic intelligence can assist the inspector search for issues whereas they’re nonetheless small.”
Modularity is a key facet of CMU system
The Carnegie Mellon workforce made modularity a precedence when constructing its crawling robotic. The drive practice, the wheels, the middle bundle, the resin, and the ability supply will be swapped out if wanted.
“Modularity permits us to construct custom-made options. In different phrases, we’ll by no means have the ability to determine what the right robotic is,” mentioned Choset. “However possibly if we determine the parts, we are able to organize and rearrange them, in order that we are able to have that proper robotic.”
“However there’s a good higher motive why you need modularity, and that’s as a result of it expedites growth,” he added. “So as an alternative of growing a brand new system each time, you simply develop a module.”
“What we’re modulating will permit the technician to say, ‘You realize, I form of like this, but when this half we’re a little bit totally different, it’d be higher,’” Choset mentioned. “And we’re going to shut the loop with the consumer and the designer and make what I believe could be an optimum answer.”
The CMU workforce plans to proceed growing totally different fashions of its robotic. Choset mentioned he hopes to carry the know-how behind the robotic to market later this 12 months with an organization he calls JP Robotics.
“I’m eager about robots on the whole; I like functions for robots in confined areas, in order that’s search and rescue, drugs, inspection of nuclear plans, and now this,” mentioned Choset. “So, to me, all of them fall collectively fairly properly. After which simply with the ability to maneuver, sense, and predict what occurs in these tight areas, I simply discover it to be a really attention-grabbing drawback.”
Be taught from Agility Robotics, Amazon, Disney, Teradyne and lots of extra.
[ad_2]