
[ad_1]
Take heed to this text |
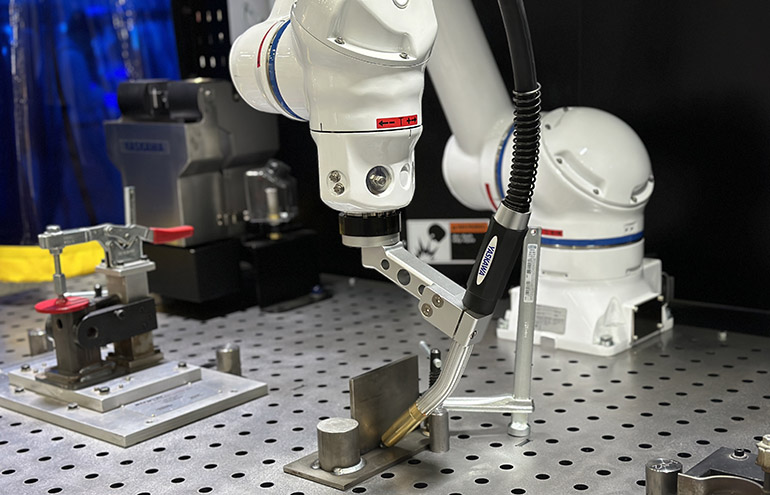
CHICAGO — Yaskawa Motoman final week confirmed a number of choices bundling its robots with imaginative and prescient and controls to assist producers undertake automation. They included collaborative and industrial robots, in addition to workcells for purposes reminiscent of welding and palletizing.
“Refined calls for and shifting markets are remodeling the commercial panorama, necessitating the necessity for good know-how and easy-to-use robots that may assist firms of all sizes simply adapt to altering manufacturing necessities,” mentioned Yaskawa.
Based in 1989, the Motoman Robotics Division of Yaskawa America Inc. offers programs for purposes together with meeting, coating, shelling out, supplies dealing with, materials slicing and removing, packaging, and scientific laboratory specimen processing.
Dayton, Ohio-based Yaskawa America Inc. touted its 4.7 (out of 5.0) approval ranking in its 2023 Buyer Satisfaction Survey.
“This degree of efficiency is a direct results of a devoted, extremely skilled crew centered on executing sound methods, producing high quality options, and delivering world-class assist,” said Steve Barhorst, president and chief working officer of Yaskawa Motoman. “This achievement validates that our company dedication to buyer assist, mixed with additional efforts by all staff, ends in happy prospects.”
Submit your presentation thought now.
Yaskawa contributes to cobot welding cells
Yaskawa confirmed how its collaborative robotic arms have gotten simpler to make use of and reprogram for a number of purposes. The firm designed the six-axis HC-Collection cobots to complement guide welding.
With companion ARC Specialties, the corporate demonstrated its AR1440 system for high-speed arc welding. The six-axis robotic has an expanded wrist movement vary and a 12 kg (26.4 lb.) payload capability. It additionally helps the featured DINSE REVO liquid-cooled rotary torch, which has a built-in slip ring for steady rotation when deep within the bore.
Yaskawa claimed that the mix of a strong 360° rotary torch, a Miller welding package deal, its personal Common Weldcom Interface (UWI) pendant software, and ARC Specialties’ programming experience offers producers with a high-production cladding choice. It additionally minimizes necessities for programming and startup, it mentioned.
The ArcWorld HC is a conveyable store for human-collaborative interplay for medium- or low-volume runs. It contains the HC10DTP cobot, which has a 1,379 mm (54. in.) most attain and a ten kg (22 lb.) payload capability.
Energy and force-limiting (PFL) know-how permits for secure operations and hand-guided programming and not using a train pendant, mentioned Yaskawa. UWI works with a number of digital welding energy provides and permits for simple management of weld processes or parameters, it famous.
For smaller components, Yaskawa’s ArcWorld LC system is designed for fabricators with lighter quantity necessities. The workstation is configured for broad components and features a mounted tooling desk with a 250 kg (551 lb.) payload or a servo-driven MH185 headstock with a 185 kg (407.8 lb.) payload.
ArcWorld has a 2,125 x 2,097 mm (83.6 x 82.5 in.) footprint, and a twin configuration is accessible. The system can slot in a trailer and features a single AR1440 robotic utilizing the UWI.
As well as, Novarc exhibited the NovEye weld monitoring and management system, which permits a robotic to adapt a programmed path based mostly on traits of the weld puddle for a correct weld.
Yaskawa additionally affords the AR-Collection robots for high-speed arc welding. These six-axis robots can deal with payloads of 8 to 25 kg (17.6 to 55.1 lb.) and assist all kinds of torches and sensors.
Motoman demos machine tending, bin choosing
With laptop numerical management (CNC) supplier Vista Automation, Yaskawa displayed the ROBOTEND system with the high-speed GP12 robotic for machine tending and parcel induction. The robotic has a 1,440 mm (56.6 in.) horizontal attain, a 2,411 (94.2 in.) mm vertical attain, and a 12 kg (26.4 lb.) payload capability.
The GP12 works with patented Good Body know-how helps decide the consumer’s orientation relative to the robotic. This makes the consumer the body of reference, eliminating the usage of standard X, Y, and Z coordinates for a sooner studying curve, mentioned Yaskawa.
The cell additionally included Plus One Robotics‘ PickOne Notion Package, which guarantees human-like imaginative and prescient for clever 3D scene capturing, in addition to decide charges over 1,600 per hour for all kinds of objects.
Yaskawa additionally demonstrated a pattern of each industrial and collaborative robots turning into extra succesful. The corporate mentioned it designed the GP8L robotic to optimize throughput in tight manufacturing areas.
The GP8L has a 1,636 mm (64.4 in.) horizontal attain, a 2,894 mm (113.9 in.) vertical attain, and a 8 kg (17.6 lb.) payload capability. It has an IP54 physique and may be mounted on flooring, partitions, and ceilings or tilted. It has brakes on all axes and is designed to optimize throughput.
A KEYENCE 3D imaginative and prescient system used sample projections and structured lighting to acknowledge randomly positioned components for quick and correct bin choosing.
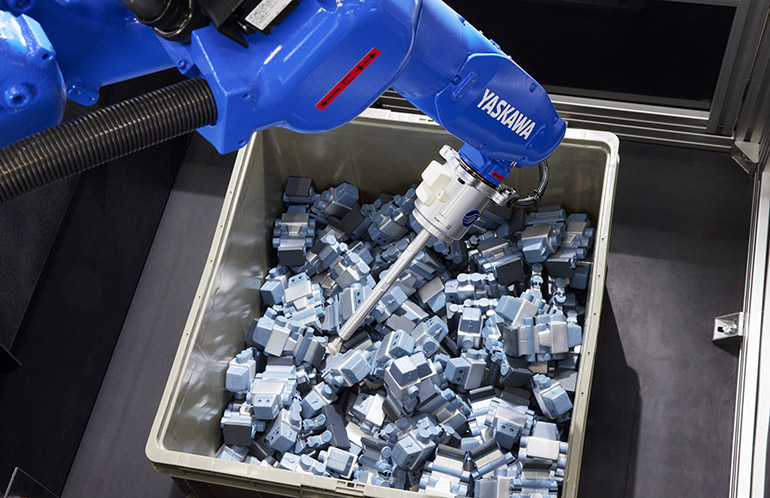
Good Pendant v3.0 designed to speed up purposes
The GP12 and HC-series robots work with Good Pendant Model 3.0, which is meant to speed up software setup. It builds on prior software program updates to permit for fast implementation of automated meeting, welding, injection molding, inspection, machine tending, palletizing, and pick-and-place duties, mentioned Yaskawa.
Good Pendant, which incorporates a number of updates to options such because the YRC1000 controller software program that may run on Home windows, is accessible to be used with choose Yaskawa Motoman YRC-controlled robots.
Palletizing and depalletizing have change into fashionable purposes to automate as a result of robots can scale back employee pressure from repetitive and heavy motion. The Pallet Builder extension to Yaskawa’s Good Pendant offers a consumer interface for “no-code” programming for workcell configuration and setup.
Pallet Builder is designed for high-mix, low-to-medium quantity manufacturing at small and midsize enterprises (SMEs), with assist for as much as eight mixed stations. Yaskawa mentioned the software program can work with all kinds of end-of-arm instruments (EOAT) and requires Good Pendant v3.0. Pallet Solver is an offline PC-based software for establishing palletizing routines.
Robotic arms get longer and stronger
Becoming a member of different heavy-duty cobots at Automate, Yaskawa’s HC30PL has a 30 kg payload and 1,700 mm most attain. It’s appropriate for palletizing and meals dealing with, in line with the corporate.
It affords 4 modes of collaborative software and may shift between PFL mode for operations round individuals to full-speed industrial mode to optimize cycle instances, based mostly on danger assessments and course of necessities.
The palletizing system additionally features a plug-and-play software flange based mostly on EN ISO-9409-1 and a thru-arm Class 6 Ethernet cable. It has an IP67 ranking and easy-to-clean floor for NSF H1-certified food-grade grease.
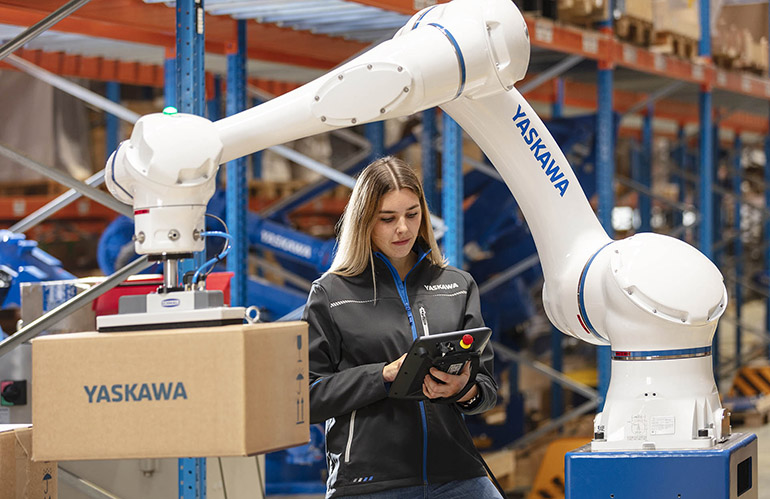
Yaskawa Drives & Movement division a part of shows
Yaskawa’s Drives & Movement division additionally displayed its merchandise at Automate. The iCube Management machine controller has an open design and modular system integration, and “offers builders the liberty to program perform modules within the language of their alternative,” the corporate asserted.
The division additionally confirmed food-grade and hygienic stainless-steel servo motors to be used with its Sigma Collection amplifiers complying with U.S. Meals and Drug Administration (FDA) and European Hygienic Engineering and Design Group requirements.
Talking of meals and beverage, thirsty convention goers may see the HC10DTP cobot, which was a part of the renovated “Yaskawa Pub.”
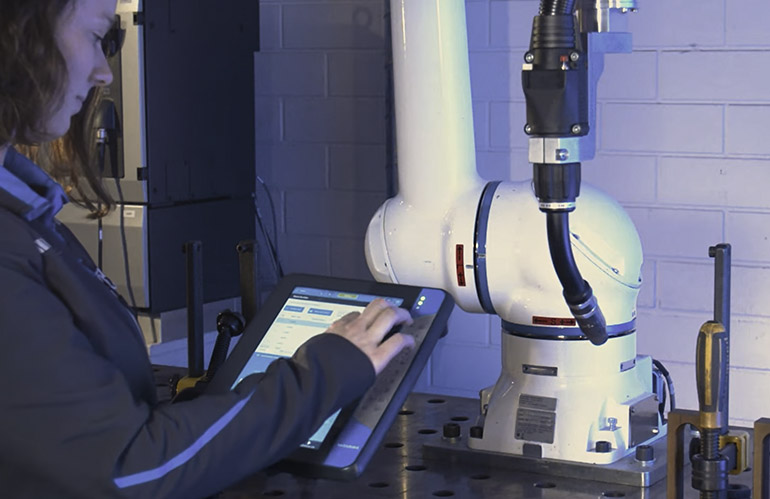
[ad_2]